Blast Furnace Slag (BFS)
Brief Description 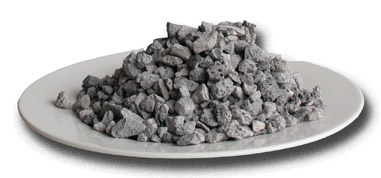
BFS is formed in a blast furnace with molten iron from iron ore in the reducing presence of heated air, coke and limestone. The resulting molten slag and iron, once removed from the furnace, are subject to further processing to form a crystalline aggregate or ground blast furnace slag (GBFS).
Physical Description
BFS is typically a grey vesicular material that is lighter than most basalt. It is pozzolanic with some self-cementing properties, that increases in proportion to the amount of fines present. Although called air-cooled slag, after initial solidification occurs in the ground bays, the slag is sprayed with water to reduce temperatures and to induce fracturing of the slag mass.
When recovered, usually with a front end loader, the slag readily breaks up with an appropriate maximum lump size of 300mm, which is then graded down to fine material. When crushed, slag fractures to an excellent cubical shape with relatively few elongated pieces.
Method of Manufacture
Within an integrated steelworks, the first step in the production of steel is to manufacture iron from iron ore. Australian iron ores are amongst the purest in the world. The iron ore, together with coke as a fuel and limestone as a fluxing agent, is fed into a blast furnace - consisting of a large vertical chamber - into the lower section where large volumes of hot air are blasted.
This process operates continuously, with the column of raw materials slowly settling as the iron is melted from the ore in a reducing atmosphere, to a molten pool around 1600°C at the bottom of the furnace. Slag - comprising of the lime from the limestone and the silicates and aluminates from the iron ore and coke - forms as the iron is reduced and the coke is consumed as energy.
Slag being lighter floats on top of the molten iron "liquid". Every two to three hours, the molten iron and slag is drained from the furnace. After separating from the heavier iron, the slag is typically tapped or poured onto ground bays to air cool.
Molten blast furnace slag, which is rapidly quenched from the furnace, air-cools slowly to form (GBFS). Where this granulated slag is further processed or ground, the product is referred to as ground granulated blast furnace slag (GGBFS).
Approximately 300kg of slag are produced for each tonne of iron. The furnace operates on a continuous daily basis with a furnace life of approximately 10 years.
Diagram of Manufacture
Applications
BFS may be used in applications to replace traditional quarried materials.
Typical uses for BFS are:
- Pavement applications
- Base & Subbase (ridge and flexible)
- Concrete Aggregate
- Filter Aggregate
- Construction fill and selected fill
- Scour protection
- Rockwool.