Granulated Blast Furnace Slag (GBFS)
Brief Description 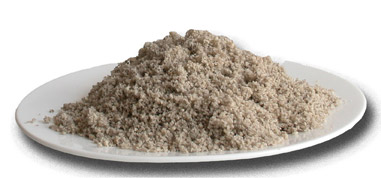
GBFS is formed when molten blast furnace slag (BFS) is rapidly quenched from the furnace, rather than left to slowly solidify by air-cooling.
Physical Description
On casual examination, GBFS would pass for river sand, with a top size of about 6mm. It typically has a density of about 60 - 70% of natural sand.
Method of Manufacture
After separating molten BFS from the molten iron, the slag can be allowed to run into or to be transported to ground bays to air-cool. There it solidifies and becomes a rock or crystalline BFS.
Alternatively, the molten slag can be quenched rapidly by passing it through a trough of high pressure, high volume water sprays, during which the heat energy contained in the molten slag causes it to explode and instantly form GBFS. GBFS is transported to stockpiles where the material dewaters prior to collection using convention front end loaders.
Diagram of Manufacture
Applications
GBFS may be used without further processing as a construction sand, soil/pavement stabilising media or grit-blasting material.
Typical uses for GBFS are:
- As a general purpose construction sand in civil engineering applications
- As an ideal select fill behind reinforced earth wall construction. Within a relatively short time, the pozzolanic properties of granulate cause it to set and form a solid block
- As a source of alumina and silica in glass manufacture
- As a stabilising agent in road construction. There have also been examples where only granulate has been used as pavement material. Pavements now exist where granulate has been used in conjunction with steel slag to form very heavy-duty pavements.
- As a grit-blasting medium: granulate is particularly suitable for soft metals such as aluminium where a light etch is required