Steel Furnace Slag (SFS)
Brief Description 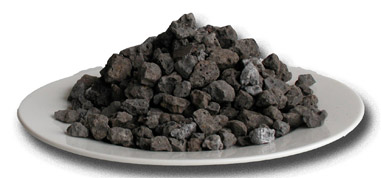
SFS is the co-product of the steel making process in the basic oxygen system (BOS). The slag is removed from the vessel after the exothermic refinement of molten iron and recycled steel in the presence of fluxes and oxygen.
Physical Description
SFS produced in the BOS is dark gray in color and characteristically harder than blast furnace slag (BFS) with a density approximately 20 - 25% greater than basalt or BFS. It crushes to a cubical shape.
BOS slag, in common with most steel slags, can be subject to slight dimensional expansion until it fully hydrates. Processors of BOS slag have developed various weathering techniques to reduce expansion potential. Care should be taken with unweathered BOS slag in highly bound (concrete) or confined spaces.
Method of Manufacture
Iron is high in carbon and is hence too brittle for many applications. As such, it is necessary to reduce the carbon content to produce ductile steel.
Conversion of molten iron to steel at an integrated steelworks takes place at the basic oxygen steelmaking shop. The BOS vessel is an open-topped container with a removable cover, in which approximately 50 tonnes of steel scrap – in addition to some 200 tonnes of molten iron brought direct from the blast furnace in brick lined ladles – is placed.
An oxygen lance is lowered into the vessel and a violent reaction takes place. Lime is added to form a protective slag layer. After the desired carbon level is achieved, components are added to the vessel to produce the required steel specification.
Upon completion of the reaction, the steel is drained into one ladle and the slag is poured into another. The ladle of molten slag is then poured into ground bays where after initial solidification, the slag is cooled with water sprays.
Diagram of Manufacture
Applications
Advantages offered by SFS free lime content have been recognised with the development of self cementing, heavy duty pavements. Unconfined compressive strength (UCS) > 5 MPa have been achieved at 28 days damp.
As a tough durable material SFS has excellent skid resistance properties compared to basalt, making it an ideal aggregate for this application. Resistance to rutting makes SFS particularly applicable for heavily trafficked corners and stopping zones.
Typical uses for SFS are:
- Sealing aggregate (skid resistant)
- Asphalt aggregate
- Rail ballast
- Pavement base and subbase layers
- Engineering construction fills
- Subsoil drains
- Grit blasting.